Adhesives for modular kitchen and bathroom furniture
Adhesives are used in a variety of ways to manufacture case furniture. This is the case, for example, for surface or profile laminating processes, edge bonding or carcass gluing. Especially for bathroom or kitchen furniture, the use of the right adhesive is crucial. This is the only way to produce furniture that can withstand external influences for years. These are primarily heat and moisture or steam. Furthermore, the right adhesive is crucial for smooth, economically efficient production. Polyurethane-based adhesives offer by far the best performance. Of course, our reactive PUR hotmelt adhesives are also available in micro-emission quality.
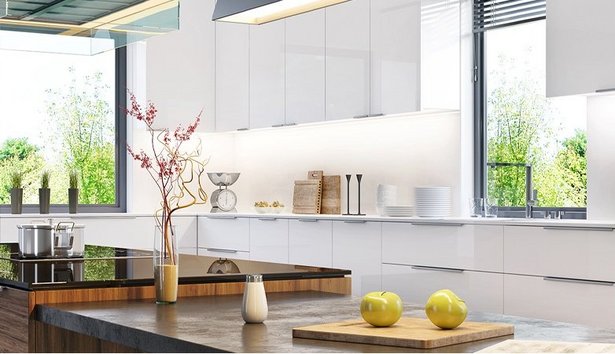
© sl-f - istockphoto.com
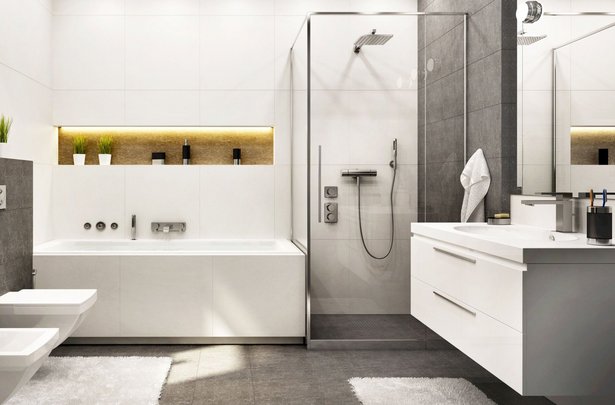
© slavun - fotolia
2D surface lamination
Adhesives for laminating furniture fronts
Modular bathroom and kitchen furniture is often made of wood-based materials such as MDF or chipboard, which is then coated with decor materials to protect the substrate and to make the product more visually appealing. Popular decors are: paper, hard-wearing laminates (CPL, HPL), PVC, ABS, PP, PMMA and PET films, and real wood veneers. There is a huge choice of decor materials available, giving kitchen designers endless design options. Elements that are commonly laminated are:
-
fronts
-
sides
-
rear panels
-
shelves
Supermatt and high-gloss decors are currently en vogue. The surfaces must be mirror-smooth, also across bonded edges and especially on thin decors, as even the smallest irregularities will impact the apearance. The surfaces must also be very resistant to moisture, heat and steam over the long term.
Our product range includes a series of adhesives specifically for high-gloss surfaces, as well as for other decors. We also offer tried-and-tested inline solutions for effective surface bonding and edge banding in a single run (e.g. the CompleteLine process).
Our engineers have decades of experience in bonding a wide variety of material combinations. They have extensive knowledge of the standard machines and application methods, and are committed to developing customized bonding solutions for and with our customers.
Would you like a personal consultation? Let us help you find the right adhesive for your needs. Contact us directly by e-mail or phone.
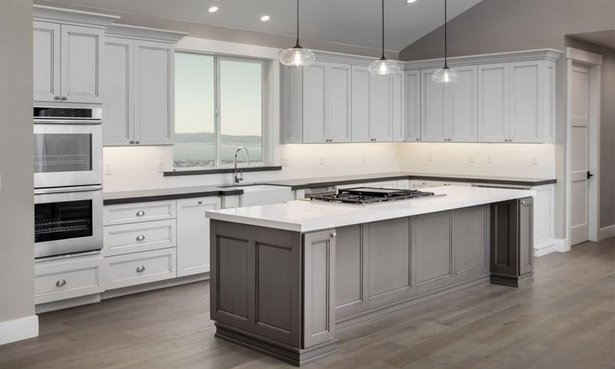
© coralimages - fotolia
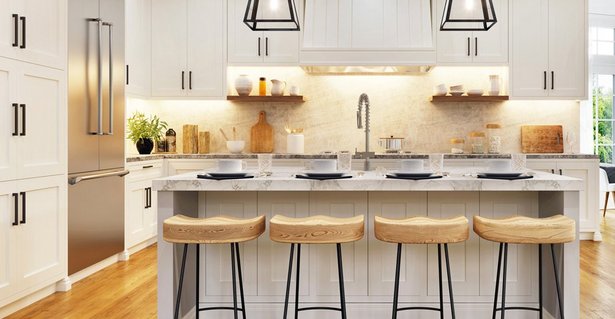
© slavun - stock.adobe.com
3D surface lamination
Kitchen and bathroom furniture sometimes has a 3D surface for aesthetic or design reasons. MDF boards are commonly used for shaker panelling, for instance. Durability is a key aspect for kitchen furniture. In kitchens as in bathrooms, the furniture is constantly exposed to heat, moisture and steam. It is therefore essential that the adhesive used to glue the decor and the substrate has the same long-lasting properties as the other materials. 3D coating is most commonly used for kitchen and bathroom fronts.
Typical material combinations are:
-
PVC films and MDF
-
PP films and MDF
-
PET films and MDF
-
ABS films and MDF
-
real wood veneers and MDF
Laminating is usually done with low viscosity, polyurethane-based 1C or 2C dispersions, using membrane or vacuum presses. With the right know-how and the right product – e.g. a PUR dispersion – even high-gloss decors and very sensitive films that do not tolerate high joining temperatures can be perfectly bonded.
Polyurethane dispersions are sprayed to the wood-based boards using a manual gun, a spraying machine, or robot technology. The adhesive is then dried, and the bonding should take place within the next 24 hours. To this purpose, the product is placed in either a vacuum or membrane press, where the decor film is applied. Temperature and pressure reactivate the adhesive, allowing the decor film to adapt to the 3D contours of the product.
PVAc dispersions (white glues) can also be used for gluing veneers. Before being pressed, the veneers are slightly moistened on the surfaces that will later be visible, to prevent any cracks or tears occurring during the pressing process. Both materials are then pressed in a membrane press.
Contact us for advice. Our engineers have a wealth of experience in dealing with the challenges of 3D lamination. Benefit from our decades of experience.
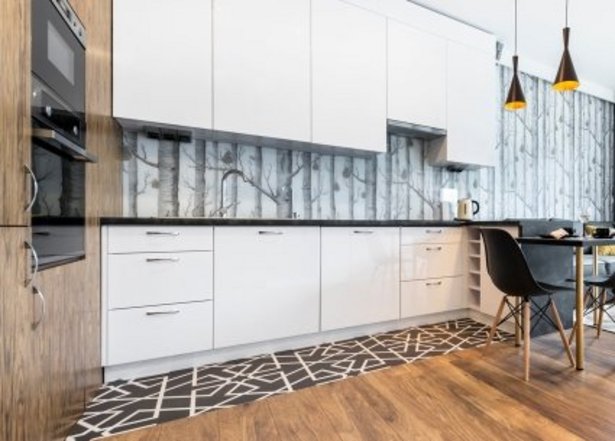
© Jacek Kada - fotolia
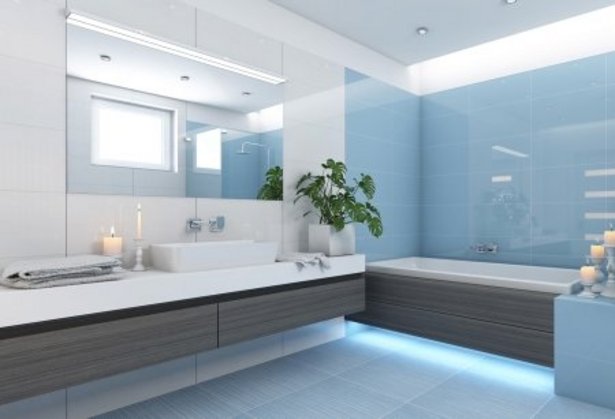
© krooogle - fotolia
Edge banding for kitchen and bathroom furniture
Edge banding gives the finishing touch to coated boards. The visible narrow surfaces are coated with decorative plastic, wood or metal edges, so that the final product looks as if it was cast in a single mould. The joints between the materials are particularly fragile, but must be made as invisible and physically tight as possible. Kitchen and bathroom furniture, in particular, is often exposed to water, steam and heat. If a badly made edge joint comes into contact with these elements, it will begin to swell and, sooner or later, ruin the whole piece of furniture.
There is a huge variety of edge banding materials on the market; plastic, metal or wood are usually used. Edge banding is used for:
-
fronts
-
side panels
-
and occasionally rear panels
The surfaces themselves are generally already laminated before edge banding is done. Typical material combinations for edge banding are:
-
MDF boards with ABS edges
-
chipboards with ABS edges
-
sandwich panels with ABS edges
-
sandwich panels with aluminium edges
-
and many more.
Nowadays, zero bond lines are the standard in high quality furniture. They stand for the highest level of workmanship and offer the best protection against moisture and other elements.
Reactive PUR adhesives are the products of choice for realizing sophisticated edge banding in kitchen and bathroom furniture. With these adhesive systems, chemical cross-linking occurs after physical curing, resulting in very high temperature resistance (-30°C to +150°C) and moisture resistance. This gives reactive PUR adhesives clear benefits over EVA or polyolefin-based adhesives. KLEIBERIT PUR hotmelts are suitable for almost all edge banding purposes.
Do you need advice on which adhesive to use or how to optimize your processes? Our engineers have extensive knowledge of standard edge banding machines. Drawing on 70 years of experience in adhesives and coating machines and methods, we have the expertise to improve your specific edge banding processes. To the products & direct contact links.
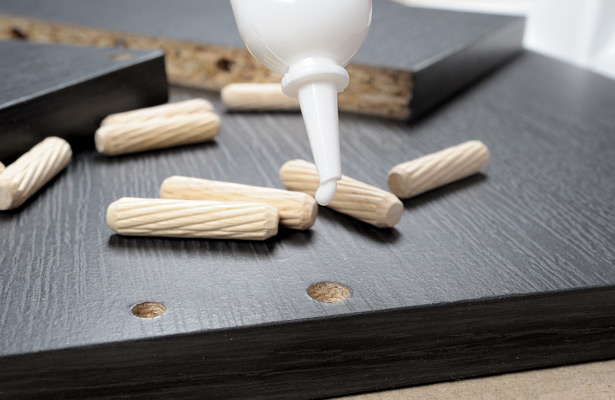
© NorGal - stock.adobe.com
Gluing dowels and furniture bodies in kitchens and bathrooms
Dowels are used to join laminated and edge-banded furniture elements, usually for corner joints, and they are often glued in. In mass production, they may be inserted with the aid of dowel insertion machines and using a special dowel glue. Either a very high viscosity or a low viscosity thixotropic dowel glue is used, depending on the intended use of the furniture and the specifics of the production process. Dowel glues are special PVAc-based dispersion adhesives that prevent the application nozzles becoming encrusted.
Would you like a personal consultation?
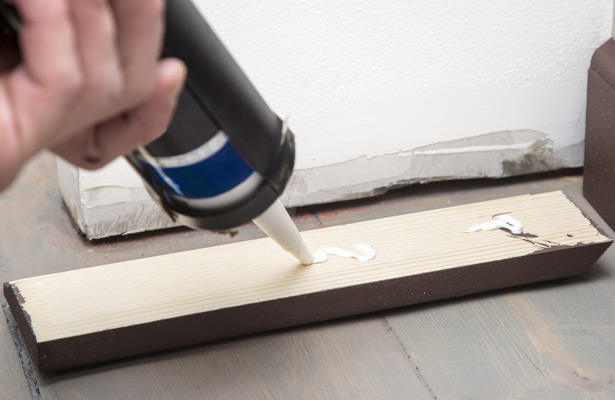
© Ronstik - stock.adobe.com
Assembly bonding
Drilling and inserting screws is time-consuming and often results in unsightly holes. With the right assembly adhesive at hand, there is no need to drill holes and install rawlplugs and screws. KLEIBERIT offers a comprehensive portfolio of assembly adhesives for:
-
gluing handles to fronts or drawers
-
mounting mirrors onto tiles (mirror gluing according to DIN 1036)
-
installing skirting boards
-
mounting protection strips on doors and walls
-
attaching decor elements
KLEIBERIT’s STP- and PUR-based assembly adhesives offer strong bonding to almost all types of materials.
New products
KLEIBERIT 706.4.54 Reactive hotmelt
- high initial strength
- medium viscosity
- surface lamination of materials with high recoil strength, e.g. veneers, HPL, CPL
KLEIBERIT 707.9.85 Reactive ME hotmelt
- no hazard labeling required, contains renewable raw materials
- for industrial equipment with higher feeding speeds
- versatile edge banding on furniture boards (fronts, rear and base panels, sides)
KLEIBERIT 736.2.00 Reactive hotmelt
- revolutionary, isocyanate-free reactive hotmelt
- sticks to a very wide range of materials
- low processing temperature
- general surface lamination
Dispersion adhesives
KLEIBERIT 332.0.00 Surface/veneer glue
- dispersion adhesive with long open time
- IMO FTP Code Part 5 & Part 2
- surface bonding of laminated panels on wood-based boards
KLEIBERIT 303.0.00 White glue
- dispersion with medium open time (6-10 minutes)
- DIN EN 204 D3
- as a two component glue with 5% KLEIBERIT 303.5.00 DIN EN 204 D4
- DIN EN 14257 (Watt 91)
- FDA Guideline 21CFR § 175.105
- surface bonding (veneer on wood-based materials)
- surface bonding of HPL and CPL to wood-based materials
- gluing furniture bodies
- gluing mortise joints
KLEIBERIT 308.0.00 Lacquer glue
- dispersion adhesive for varnished surfaces
- bonding wood-based materials to varnished surfaces
KLEIBERIT 316.0.00 Dowel glue
- non-blocking PVAc dispersion for use with doweling machines with injection nozzles
- gluing furniture bodies with automatic dowelling machines
- knot-sealing machines
KLEIBERIT 431.7.00 1C PUR dispersion adhesive
- THE high-gloss expert
- FIRA certified according to BS 6222 Part 3 1999
- 3D film lamination for high-gloss and thin films
KLEIBERIT 433.2.00 Supratherm - 2C PUR dispersion adhesive
- all-round product for all standard deep-drawing processes
- 3D film lamination for all standard films, usable with or without a hardener
KLEIBERIT 438.7.00 1C / 2C PUR dispersion adhesive
- for automatic application systems
- 3D film lamination with automatic application systems
- very homogeneous spray pattern, for thin and high-gloss films
KLEIBERIT 453.0.00 Film glue
- surface lamination with PVC and paper films, with presses and in continuous processes
KLEIBERIT 464.8.00 dispersion adhesive
- wrapping drawer jambs with PVC films
- surface lamination of PVC furniture films and decor papers
Reactive PUR hotmelts
KLEIBERIT 706.0.00 Reactive hotmelt
- all-round product with long open time
- high initial strength
- general surface lamination
KLEIBERIT 706.0.09 Reactive hotmelt
- monomer-reduced
- no blistering
- FDA Guideline 21CFR § 175.105
- surface lamination
KLEIBERIT 706.1.00 Reactive hotmelt
- all-round adhesive with good initial strength
- sticks to a wide range of materials
- general surface lamination
- surface lamination of materials with increased recoil strength (HPL, CPL)
KLEIBERIT 706.1.50 Reactive ME hotmelt
- free of labeling
- high initial strength
- IMO FTP Code Part 5 & Part 2
- general surface lamination
- high-gloss and super matt decors
KLEIBERIT 706.2.50 Reactive ME hotmelt
- free of labeling
- excellent high-gloss properties
- general surface lamination
KLEIBERIT 706.4.00 Reactive hotmelt
- very high initial strength
- surface lamination of materials with high recoil strength, e.g. veneers, HPL, CPL
KLEIBERIT 706.7.50 Reactive ME hotmelt
- free of labeling
- high initial strength
- surface lamination of cover materials such as HPL, CPL
- impermeable materials, e.g. HPL
KLEIBERIT 707.9.00 Reactive hotmelt
- for industrial equipment with higher feeding speeds
- versatile edge banding on furniture boards (fronts, rear and base panels, sides)
KLEIBERIT 707.9.40 Reactive hotmelt
- highest possible initial strength
- ideal for CNC machines
- versatile edge banding on furniture boards (fronts, rear and base panels, sides)
KLEIBERIT 707.9.50 Reactive ME hotmelt
- free of labeling
- for industrial equipment with higher feeding speeds
- versatile edge banding on furniture boards (fronts, rear and base panels, sides)
KLEIBERIT 707.9.54 Reactive ME hotmelt
- high initial strength
- free of labeling
- versatile edge banding on furniture boards (fronts, rear and base panels, sides)
KLEIBERIT 707.9.85 Reactive ME hotmelt
- no hazard labeling required, contains renewable raw materials
- for industrial equipment with higher feeding speeds
- versatile edge banding on furniture boards (fronts, rear and base panels, sides)
KLEIBERIT 709.1.00 Reactive hotmelt
- excellent adhesion to inorganic materials
- surface lamination of mineral materials (e.g. stone veneers), metal, and glass
KLEIBERIT 709.1.50 Reactive ME hotmelt
- free of labeling
- profile wrapping
- general surface lamination
- with integrated adhesion promoter for metal surfaces
KLEIBERIT 709.3.00 Reactive hotmelt
- very high surface smoothness and quality
- high-gloss decors
- super matt decors
KLEIBERIT 711.2.00 Reactive hotmelt
- plastics specialist
- surface lamination of various plastic films
KLEIBERIT 711.3.00 Reactive hotmelt
- for gluing diffusion-resistant materials
- high initial strength
- general surface lamination
KLEIBERIT 711.3.57 Reactive ME hotmelt
- particularly suitable for bonding impermeable materials
- very good PVC adhesion
- general surface lamination
KLEIBERIT 711.9.00 Reactive hotmelt
- long open time
- extremely high initial strength
- surface lamination of materials with high recoil strength, e.g. veneers, HPL, etc.
- honeycomb plate panelling
KLEIBERIT 711.9.06 Reactive hotmelt
- for porous and pressure-sensitive materials
- very high initial strength
- surface lamination of materials with high recoil strength, e.g. veneers, HPL, etc.
- honeycomb plate panelling
KLEIBERIT 716.8.00 Reactive hotmelt
- plasticizer stable
- excellent adhesion to PVC
- general surface lamination
- surface lamination of plasticized materials on carrier boards
KLEIBERIT 716.8.50 Reactive ME hotmelt
- product free of labeling
- plasticizer stable
- excellent bonding to plastics
- general surface lamination
- surface lamination of plasticized materials on carrier boards