Adhesives for automotive interior lamination
Sound insulation and, above all, pleasant haptics make for a pleasant user experience in modern vehicles. Modern cars are made of the latest new and increasingly lighter materials, usually in very high quality.
Adhesives used in the automobile sector have to meet extremely high standards. Depending on the location and season, even vehicle interiors can be exposed to extreme climate differences. Car manufacturers also have to cater for complex manufacturing processes and ever shorter processing windows.
Demand for improved workplace and environmental safety is increasing the need for low-emission adhesives with low monomeric isocyanate content. The end products, too, have to comply with strict emission standards when in use. All these factors mean that vehicle manufacturers and suppliers need smart and effective adhesive solutions they can rely on.
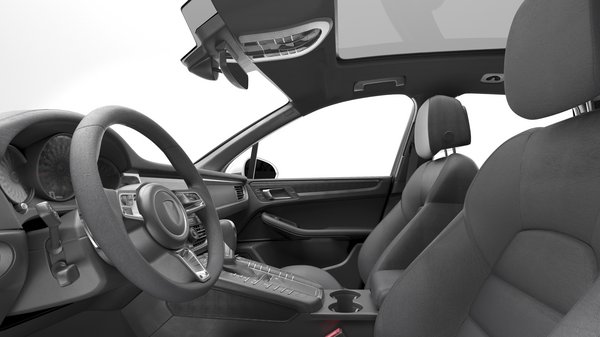
© Cyprych Kalienke
Laminating vehicle interiors involves bonding a variety of different materials. When in use, these parts are constantly subject to varying temperatures and humidity levels, vibrations, and even the behavior of the vehicle’s occupants. The choice of adhesive therefore plays a decisive role, also in terms of ensuring high process reliability. Typical applications for laminating vehicle interiors include:
- instrument panels & cockpits
- middle consoles
- seat backs
- door panels
- roof linings
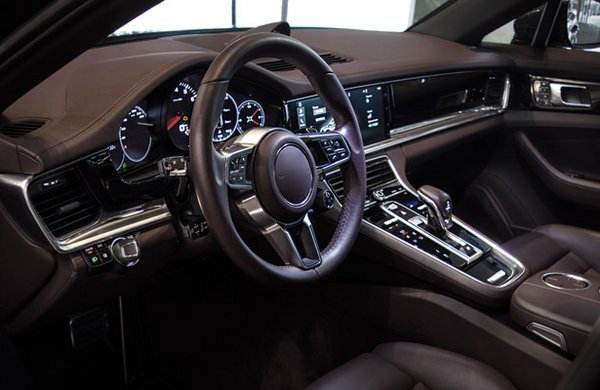
© Krystyna Taran - shutterstock.com
Good aesthetics and haptic quality are important. The carrier material is usually made of light, stable plastics or fibre composites – e.g. fibre glass or plant-based fibre materials such as hemp or flax –
and laminated with decor materials. Interior designers have a huge variety of materials to choose from, ranging from textile fabrics to imitation and real leather. Imitation leather decors lined with foam are currently popular: they are relatively inexpensive, but have an excellent look and feel. They are also sound-absorbing, which has a positive impact on the acoustics inside the vehicle. Typical material combinations are:
Carrier material:
ABS
PC
PP
fibre composites
Decor materials
PVC/TPO
imitation leather films
textile laminates
real leather
Almost any kind of material combination can be glued with the right adhesive at hand. Let us help you find the ideal adhesive solution for your individual needs – tailored to your products and production processes. Get in touch with our experts.
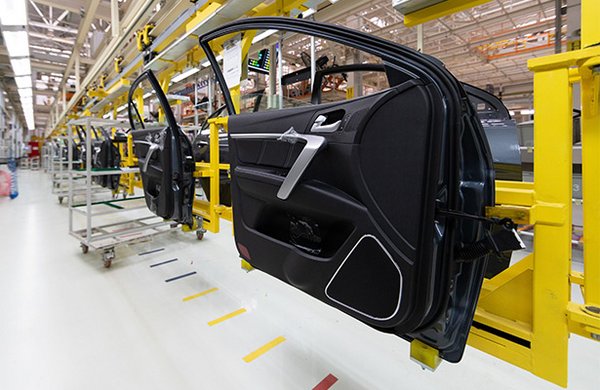
© Ivan Traimak - stock.adobe.com
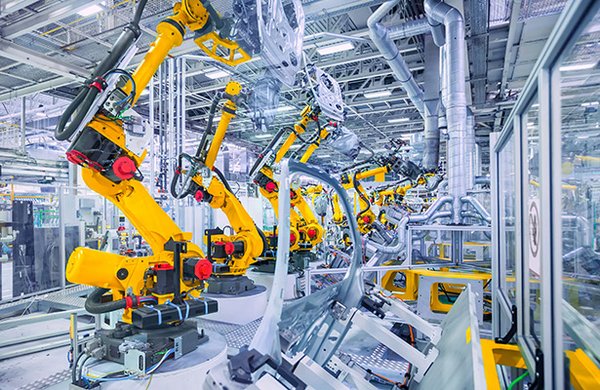
© Nataliya Hora - stock.adobe.com
High-quality and economically efficient bonding requires meticulously planned processes. The key to success is well-configured equipment with a matching adhesive formulation. If short cycle times are a factor, the adhesive must be easy to apply and have a high initial strength. We recommend using reactive PUR hotmelts for laminating vehicle interiors. They are customizable and meet the specific needs of the end product as well as the complex specifications of manufacturing processes.
A typical laminating process for an instrument panel using a PUR hotmelt involves the following stages:
1. The adhesive is applied to one of the parts to be bonded. This is done either with spray heads, rollers or slit nozzles, and can be stuck to individual cuts of the decor material or to meter goods in a roll-to-roll process.
2. The decor and the carrier material are joined under pressure and by applying heat, with the latter reactivating the adhesive. Molding presses (negative/positive molds) and vacuum forming presses are used for this purpose. At this point of the process, and especially when opening the press, it is vital that the adhesive has a high initial strength while still warm. This is particularly important for edge wrapping.
The chemical reaction (cross-linking with moisture) creates an extremely strong and very resilient bond.
The legally permitted emission values in production environments are constantly being lowered, and adhesive manufacturers have to adapt their products accordingly. Users can rest assured of high workplace safety when working with our micro-emission (ME) adhesives. Due to the low content of monomeric isocyanate (<0.1%), hazard statements G + H no longer apply, which eliminates the need for many safety requirements and the related expensive equipment and time-consuming trainings.
We have a selection of adhesive systems for use in vehicle interiors and the matching expertise. Benefit from our decades of experience in industrial manufacturing and let us help you optimize your production process.
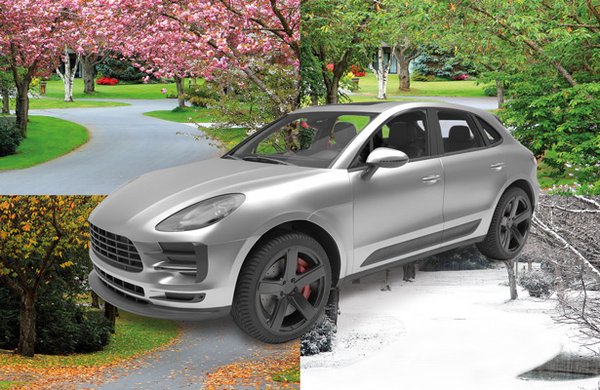
© Barbara Helgason, Cyprych Kalienke
An adhesive bond must be made to last ... for the entire lifecycle of the vehicle. Weather extremes, direct sunlight, vibrations and static loads must not have any negative impact on the bonding, regardless of the materials used. The following properties are essential for adhesives used in vehicles:
- short open times for short cycle times
- high initial strength, e.g. for complex edge wrapping applications
- permanent resistance to heat, cold, moisture, mechanical wear and tear
- low emissions (VOC, fogging, odors)
- high impact resistance (airbag release)
Benefit from our know-how. Our engineers have decades of experience with industry-standard equipment and application methods. Together with our customers, we are constantly researching new adhesives and application technologies.
Take a look at our product overview and contact us for more advice.
Highlights
KLEIBERIT 703.3.50 Reactive ME Hotmelt
- lamination in automotive interior
- assembly bonding
KLEIBERIT 713.4.54 Reactive ME hotmelt
- lamination for trunk loading floors
KLEIBERIT 713.7.50 Reactive ME hotmelt
- lamination in automotive interior
KLEIBERIT 713.7.54 Reactive ME hotmelt
- free of labeling
- very high initial strength
- excellent stability on rollers
- laminating the back shells of seats
KLEIBERIT 713.7.84 Reactive hotmelt
- micro emission
- 38 % share of bio-based raw materials
- lamination in automotive interior
KLEIBERIT 713.7.85 Reactive ME hotmelt
- micro emission
- approx. 42 % bio-based raw materials
- lamination in automotive interior
Polyolefin hotmelts
KLEIBERIT 724.1.00 Reactive hotmelt
- high initial strength
- moderately long open time
- general assembly and surface bonding in automotive interiors
KLEIBERIT 724.2.00 Reactive hotmelt adhesive
- high initial strength
- short open time
- assembly bonding in automotive interior
KLEIBERIT 724.5.00 Hotmelt
- high initial strength
- laminating glove compartment hatches
KLEIBERIT 750.0.00 Hotmelt
- high initial strength
- moderate short open time
- very good adhesion to different plastics
- assembly and surface bonding in automotive interiors
Reactive PUR hotmelts
KLEIBERIT 703.3.33 Reaktiver Schmelzklebstoff
- extremely high initial strength
- laminating instrument panels
KLEIBERIT 703.5.00 Reactive hotmelt
- high initial strength
- excellent bondig on materials that are hard to glue
- assembly bonding for operating keys
- room darkening roller blinds
KLEIBERIT 706.0.09 Reactive hotmelt
- low emission
- middle console cladding - wooden roller blinds (wood on non-wovens)
KLEIBERIT 713.0.00 Reactive hotmelt
- long open time and high initial strength
- low-emission
- boot loading floor
KLEIBERIT 713.7.00 Reactive hotmelt
- low-emission
- long open time and high initial strength
- 3D lamination applications
- boot loading floor